We have already seen many supply chains effected because of the pandemic. The latest one to see disruption is the new car market, which has seen major shortages due to lack of parts, particularly electronic components, which are being used in rapidly increasing volumes driven by the increases in electric vehicles.
When automotive production lines were brought to a halt for the first wave of lockdowns in 2020, manufacturers diverted devices that would normally go into new cars to the consumer electronics, which saw an increase in demand due to home working. However, it didn’t take long for car production to start increasing again, but the supply chain is yet to catch-up with demand with experts anticipating disruption to go well into 2022.
Semiconductor shortages
Prior to the pandemic we were already seeing an increase in demand for semiconductor devices due to the rise of 5G. When the pandemic hit, many began to stockpile and leave other companies struggling to get hold of components. The requirement for home working tech also increased demand, and now manufacturers have been left to catch-up.
When the semiconductor industry was forced to partly close because of the pandemic, the result was smaller build quantities. However, because cars are now so technologically advanced there require numerous semiconductor devices. This, coupled with the demand for chips in consumer electronics such as phones, tablets, and games consoles has caused major lead-time increases.
New cars are particularly reliant on computer chips, they control several features in new cars, such as safety devices like airbags, and automatic parking assistance. In some tech-heavy models, they can use over 40 chips from multiple manufacturers.
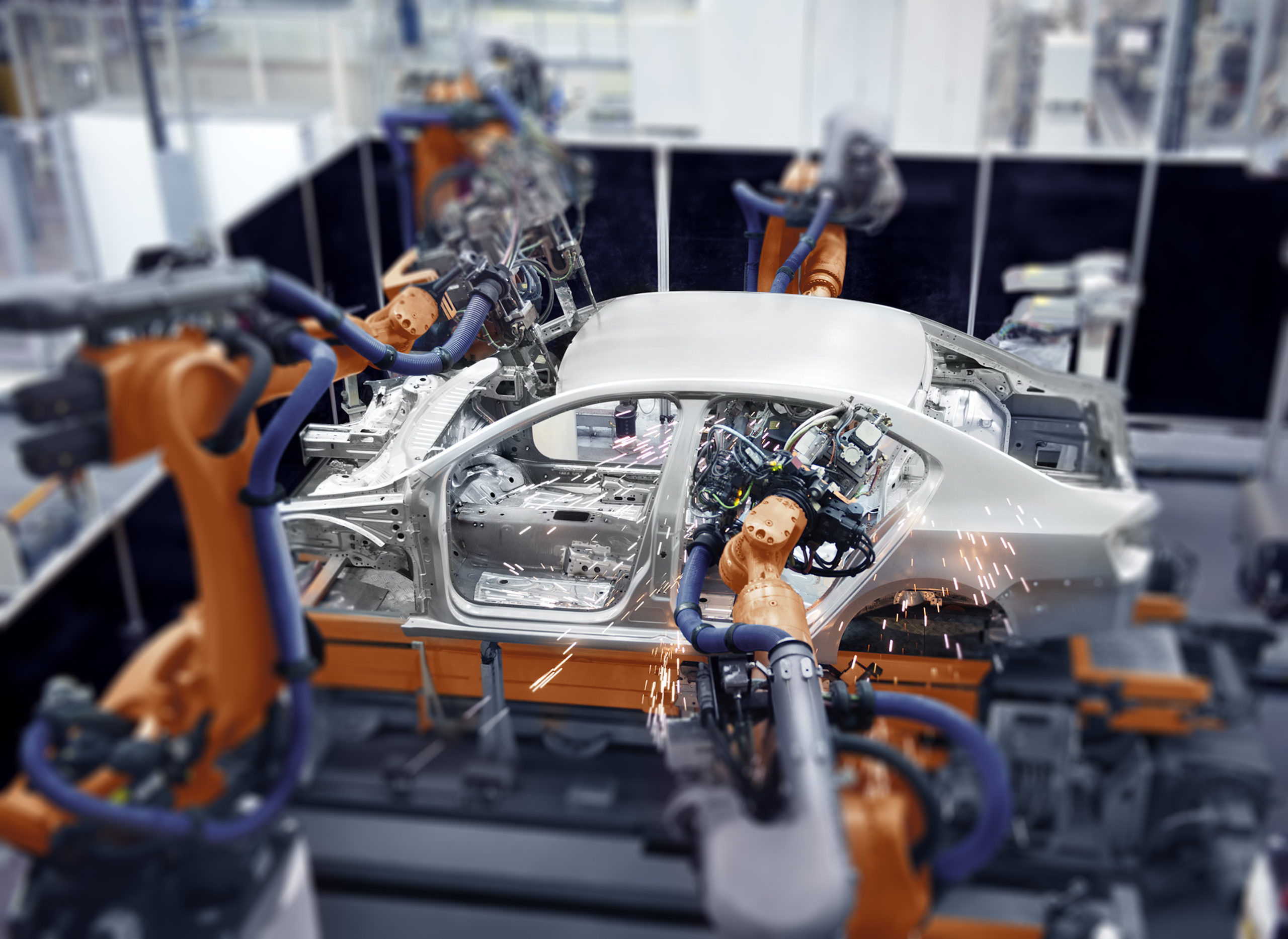
Why can’t we just make more semiconductor devices?
Semiconductor fabrication facilities take years to build and billions of pounds. The production process is lengthy too. The factories making the parts need to be ultra clean, completely dust free and void of any static electricity.
Further to this, silicon, a key material, most frequently used in semiconductors is also facing shortages due to temporary factory closures and local lockdowns. As plants begin to reopen and electronic goods producers continue to place orders, an ever-increasing backlog will continue to be created.
The future for Semiconductors
This has been described by many as a chip shortage unlike any other. Lead times are constantly changing. From January to April of 2021, semiconductor IC lead times increased 75% on average. Because of this many companies are beginning to build bigger component inventories than previous years. Which will not help the situation.
A focus on planning and proactive order management systems will ensure purchasing departments can stay ahead in what has become a very competitive industry. Many car manufacturers are now advising delays for new models of up to 6 months.